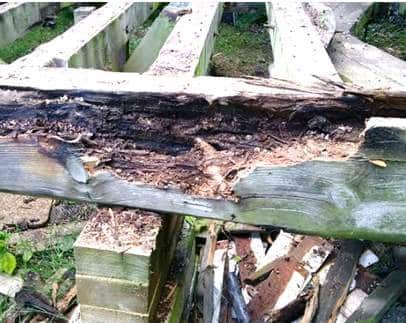
ROTTEN TIMBERS COULD COME CRASHING DOWN
In 2013 a routine inspection of the structure and working parts of the cap identified the headframe timbers were badly rotten and it’s safety was in serious doubt. The principal timbers are two sheer beams that support the weight of the fantail platform, the sails, the weight of the machinery and the cap estimated in total to be 12 tons. And so something had to be done!
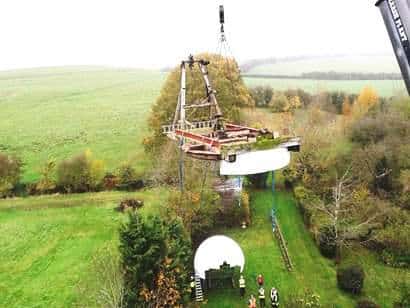
KEEPING THE HEADFRAME IN ONE PIECE
The main concern was that as the head frame was lifted by a crane the rotten timbers may collapse under its own weight. Ideally the head frame was required intact at ground level so it could be used as a pattern for it’s replacement. To achieve this the large visible cracks in the timbers were filled with cement and a long ‘rolled steel joist’ (RSJ), was strapped to each sheer beam.
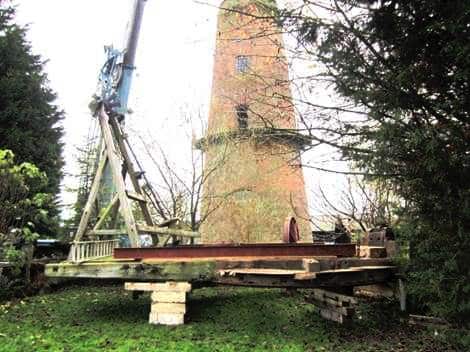
RENOVATING THE HEADFRAME
The reinforcement of the concrete infill and RSJs was successful and the headframe was successfully lifted down and placed on a frame to provide a safe working environment for it’s restoration.
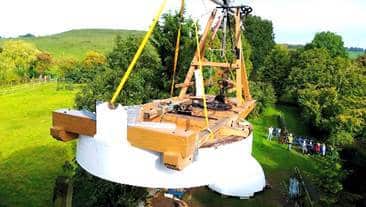
HEADFRAME
All the timber of the headframe was in poor condition and it was decided to replace it entirely. We chose oak which was delivered directly to Empringhams of High Wycombe, they manufactured it in their workshop, then dismantled and transported to Quainton to be assembled on-site.
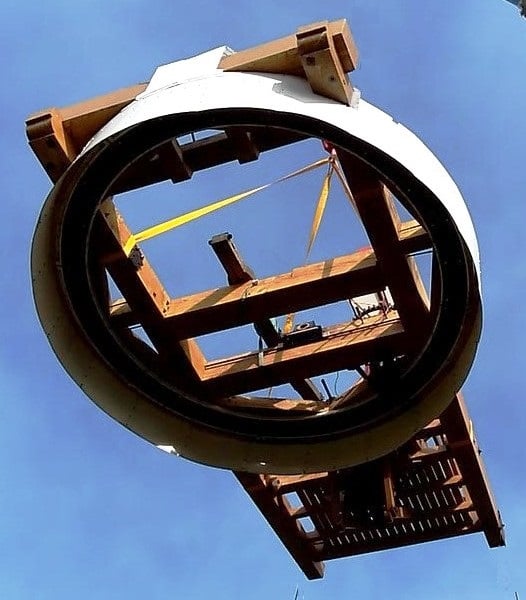
SIZE
The red and white fantail looks insignificant when viewed from a distance, however a person can safely stand under the rotating blades.
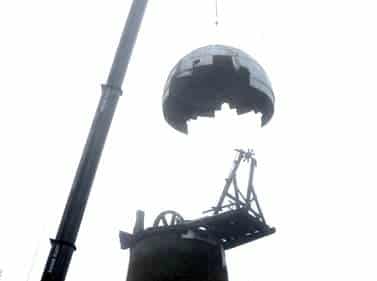
EXAMINING OTHER EQUIPMENT
The removal of the headframe gave us an opportunity to remove all the other components at the top of the mill to assess their state of repair. Our objective was to ensure the mill would be fit for purpose for many years to come.
There was a lifting eye located at the top of the dome. Once removed, the dome was placed onto a scaffold structure to facilitate a working platform to repair and renovate the panels.
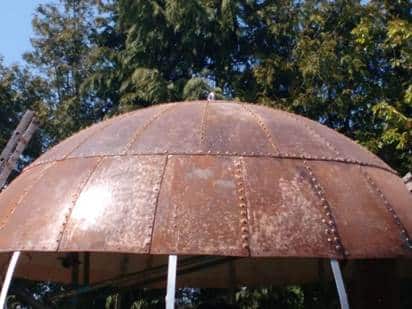
REFURBISHING THE CAP
When we started to strip down the cap we discovered it was in two parts. We were surprised the top panels, made of shaped wrought iron, were originals from 1832. These were stripped down to bare metal and painted with a bespoke paint system.
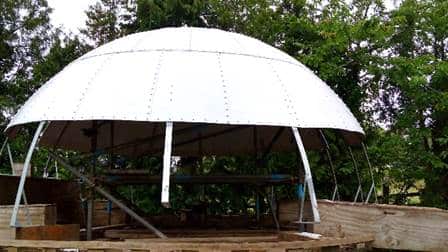
REFURBISHING THE CAP
The bottom two rows of the cap were glass reinforced plastic (GRP) panels which had been used to replace the original wrought iron, presumably to save weight and cost. We replaced them with Acrylonitrile Butadiene Styrene (ABS) plastic sheets formed to the shape of the cap. ABS is a common thermoplastic polymer typically used for vacuum forming applications.
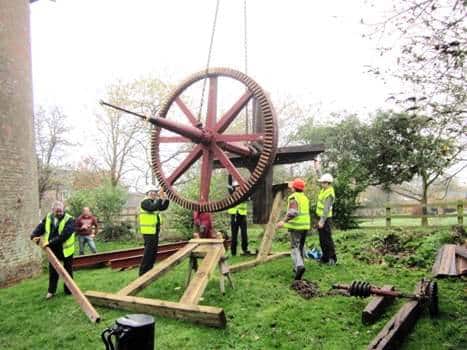
OTHER EQUIPMENT REMOVED
We removed the brakewheel and wind shaft, which was lifted off as a single component. It was lowered onto a wooden frame specifically designed to match its shape and weight. It was found to be in good condition, only required cleaning and a fresh coat of paint.
In the upper photograph, on the ground, is the worm drive and crown wheel which are part of the cap and they transfer the gearing from the fantail to the toothed rail shown in the lower picture to drive the rotation of the headframe.
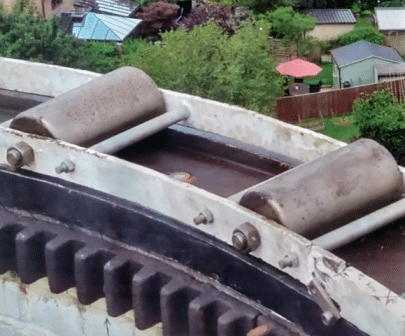
ROLLER BEARINGS (AFTER RESTORATION)
The fantail allows the cap to rotate to ensure the sails are always facing directly into the wind. This is possible because at the top of the tower are large cast iron bearings, like rolling pins, that are fixed in position in the circular steel cage, as shown over.
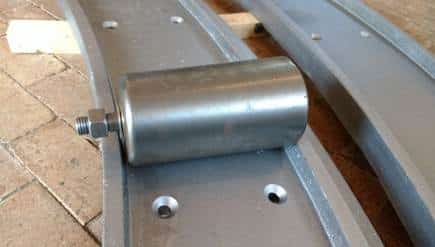
TAPERED ROLLER BEARINGS
The 24 bearings, which dated back to 1832, were in good condition with minimal wear. All of the bearings were machined to be the same size by removing a thin layer of material. The bearings are tapered to replicate the different circumferences of the outer and inner edges of the tracks in relation to the centre of the mill. The wider (outer) face is 139mm in diameter and the smaller (inner) face 123mm with a taper angle of 1.82°.
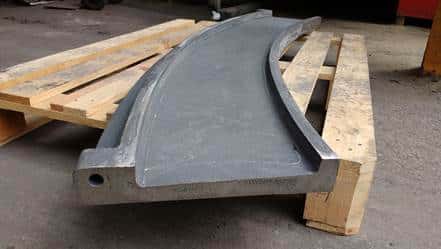
CASTING NEW TRACKS
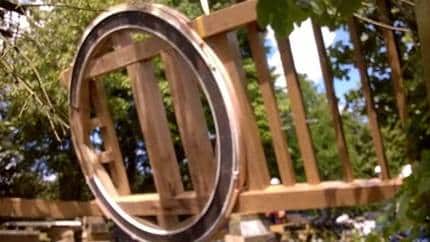
The same taper angle of 1.82° is used on the tracks as that used on the bearings to ensure smooth running.
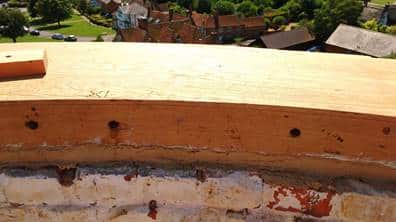
BRICKWORK & WOODEN TRACK CURB
The brickwork at the top of the tower was made good and then a new oak curb was fitted. The lower tracks are held in place using large screws plus each track section has a long bolt that passes down the inside of the brick tower wall.
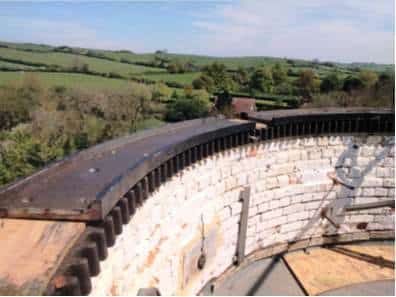
TOOTHED RACK
The toothed rack, which is original from 1832, is fitted onto the inside of the wooden curb. It was scrubbed clean and was in such good condition that it could be retained.
The drive from the fantail passes down and into the cap dome to engage with the worm drive and crown wheel. This in turn rotates a small spur wheel which engages with the rack to ensure the sails are always facing directly into the wind.
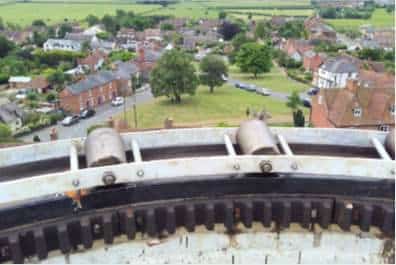
TRACK CAGE
A cage holds the newly machined tapered roller bearings at equidistant positions around the track. Once this work was complete it was possible for two men to turn the roller bearings in their cage around the track curb so that the free movement and alignment could be checked and confirmed.
HEADFRAME, FANTAIL & CAP – 19 SEPTEMBER 2017
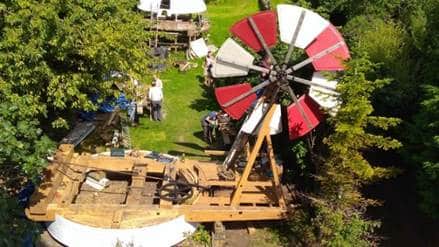
NEW HEADFRAME & FANTAIL
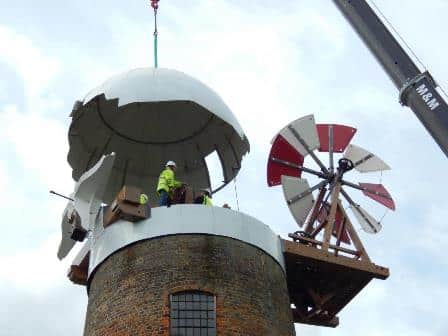
RENOVATED CAP
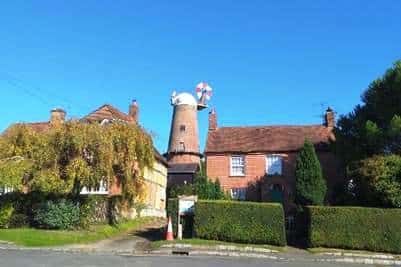
PROVING THE FANTAIL & CAP WORK
All equipment was in place; the Technical Team waited for the fantail to rotate the cap into the wind. It was vital the drive from the fantail engaged with the toothed rail around the full rotation of the headframe.
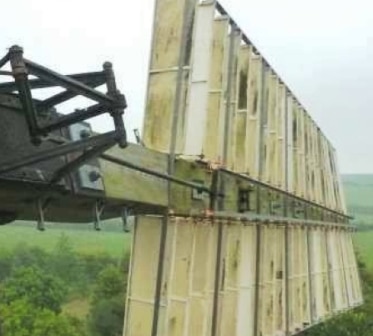
SAIL SHUTTERS
There are 168 shutters on the mill, 42 on each sail.
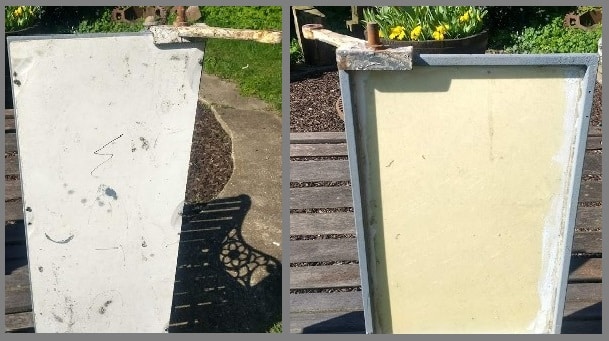
CONDITION OF SHUTTERS IN 2013
When we started the refurbishment of the original shutters, which were 14 years old, they had become badly discoloured and a number were damaged, as can be seen over.
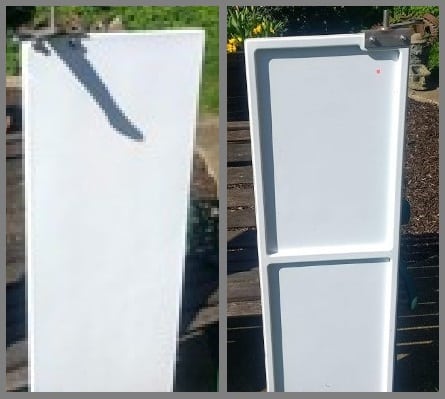
MATERIALS USED UP TO 2013
They were made with a galvanised steel frame covered with glass reinforced plastic (GRP) sheets and fixed with stainless steel pop rivets.
MATERIALS USED IN 2019
The new shutters used the existing galvanised steel frame and two new acrylonitrile butadiene styrene (ABS) plastic sheets glued together. ABS plastic was chosen because it is weatherproof, colour fast and lighter than the previous GRP.
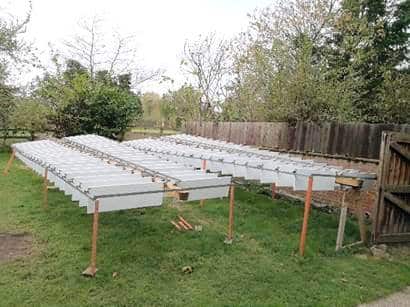
RESTORING THE SAILS
Each sail is made of two large timbers known as the whip and stock. We retained the whips and stocks and fitted them with new shutters and sail furniture.All four sails were assembled at ground level to the north and south of the mill.
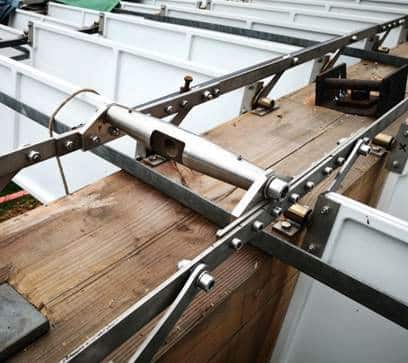
A significant number of the old cast iron operating brackets and levers were damaged and all new items were manufactured in stainless steel with nylon bushes inserted into all pivot points to aid opening and closing of the shutters.
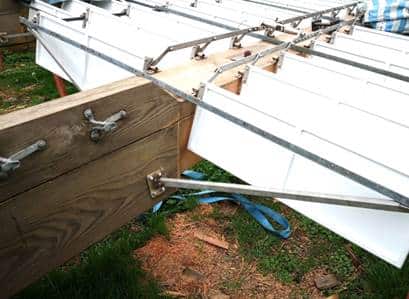
It was decided to re-introduce new stainless steel back stays fitted to the frame to stop the shutter assembly twisting on the whip and stock.
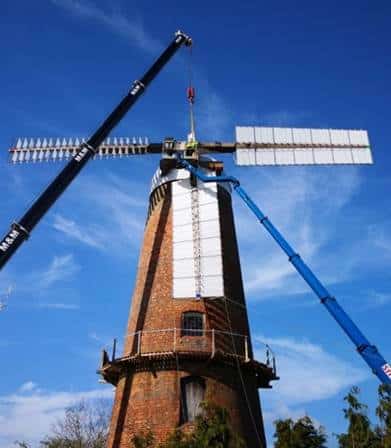
SECOND BIG LIFT FOUR SAILS – 26TH MARCH 2019
Each sail is made of two large timbers known as the whip and stock. We retained the whips and stocks and fitted them with new shutters and sail furniture.All four sails were assembled at ground level to the north and south of the mill.
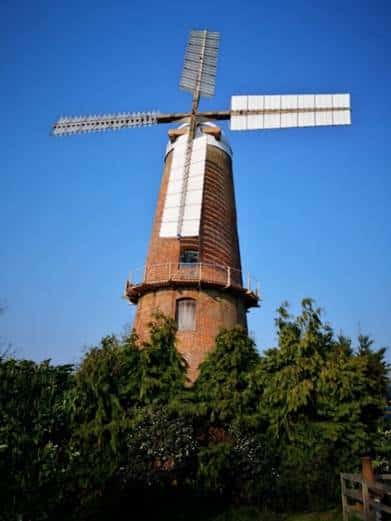
SPIDER COMPLICATION
Unfortunately the locating holes for the spider did not line up and so the spider could not be fitted during this period. A couple of weeks later the spider was fitted successfully.
THE SAILS TURN FOR FIRST TIME – 14TH APRIL 2019
On the 14th April 2019 the sails turn for the first time in over seven years, with a new head frame, a renovated cap and dome, an improved weather angle on the whips, a complete new set of shutters, and complete new set of shutter operating mechanism.
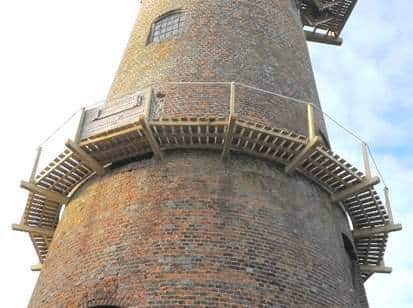
GALLERY
In September 2018 a new gallery was completed, funded by the HS2 Community Fund. This is a fund available to communities on the route of the new high speed train service being built between London and Birmingham.
The sails turned for first time in seven years on 14th April 2019.
IDEAL ROTATION SPEED
Ideal rotation is a sail passes every second.
A 10mph wind is required to rotate the sails.
MILL STONES TURNING (WITHOUT CASING)
Aug 2019 – Mill stones turning for the first time.
Jan 2020 – Flour produced in test quantities.